Types of Insulation
Insulation Perth is a key component in creating energy efficient homes. It reduces heating and cooling costs and improves comfort by regulating temperatures.
Insulating materials resist heat flow through conduction, radiation and convection. They can be either rigid or loose fill.
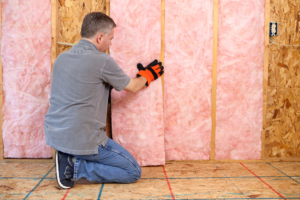
Foam insulation is blown in to walls and ceilings during construction and has high R-values, but needs to be installed correctly for best results.
Insulation Types
Many different types of insulation are available to homeowners and builders. The type of insulation best suited to your home depends on your climate, the structure of your house and the level of R-value you need. It is important to choose the right type of insulation to save energy and create a healthy environment in your home. When selecting insulation, be sure to consider the R-value, which is a measure of resistance to heat flow and can be found on the product packaging. The higher the R-value, the more efficient the insulation.
There are also green options available to help you reduce your environmental footprint. These insulation products have been tested using Life Cycle Assessment (LCA) — a technique that evaluates the environmental impact of materials throughout their entire life, from raw material extraction to manufacturing, use and disposal. LCA can help you make a more informed decision about which insulation to select for your home.
Some types of insulation are made from recycled materials, while others have a lower embodied energy and some even produce negative ions. However, some of these materials may still contain chemicals such as flame retardants or pesticides, so it is essential to read the product labels carefully.
Blanket insulation is the most common type of insulation for homes and comes in rolls or batts that consist of flexible fibers, usually fiberglass. Other forms of blanket insulation include cellulose, mineral (rock and slag) wool and natural fibers such as cotton or sheep’s wool. There are also several varieties of loose-fill insulation, which can be blown in wall cavities or attics and includes cellulose, fiberglass, vermiculite and perlite.
Loose-fill insulation typically requires experienced installers to achieve the desired density and R-value. In addition, this type of insulation is often not suitable for some areas of the home such as attics or walls.
Some insulations are manufactured as a component of a building, including insulated concrete forms and Structural Insulated Panels (SIPs). These are often used in new construction, but can also be installed in existing walls. Other types of insulation are made from foam and can be sprayed in place with a special equipment or in small containers for homeowner installation.
Vapor Barriers
Vapor barriers help prevent moisture-laden air from entering insulated wall and floor assemblies. When moisture is allowed to migrate through insulation and into the assembly, it can dampen or even rot the materials that it comes into contact with. As a result, these areas may become breeding grounds for mold and mildew. This is particularly problematic in crawl spaces where the resulting moisture can cause wood rot or contribute to fungus in concrete floor slabs and walls.
When used in a properly designed and built home, vapor barrier membranes can greatly reduce the risk of mold and mildew and provide long-term protection for the building’s foundation and subfloor. In addition, the vapor retarders that are part of the system can significantly reduce energy costs by limiting air flow through the structure and helping to control temperature fluctuations.
The need for a vapor barrier or retarder is determined by climate and the conditions in which the building will be constructed. In areas of significant annual rainfall and humidity, a vapor barrier is important to prevent ground moisture from infiltrating into the foundation and lower structural components, which can promote condensation in wall cavities and encourage mold and mildew. In arid climates, the need is less apparent, but using a vapor retarder in wall and floor assemblies can still help prevent the loss of thermal efficiency caused by condensation within insulation.
A vapor barrier is generally defined as any material that has a permeance level of 0.1 or less per square foot, meaning it is completely impermeable and will not allow water to pass through it. This can include a variety of materials including polyethylene film, foil-faced insulated sheathing and asphalt-backed kraft paper facing on fiberglass batt insulation. The vapor barrier must be attached to the sheathing at all penetrations and seams, and should be sealed tightly to ensure that it is not punctured or torn during construction.
Some manufacturers produce a product that is both an air barrier and vapor retarder and use the term interchangeably. However, these products have different functions and are best suited for specific applications. Air barriers stop vapor diffusion but do not prevent airflow, which contains 50 to 100 times more moisture than the water transported by vapor diffusion.
Vapor Retarders
Vapor retarders prevent moisture from condensing inside walls, ceilings and floors. Building occupants, appliances, plants and plumbing equipment all generate moisture that moves in the air as vapor, and this can move into insulation assemblies and wall cavities. The vapor can then find cold temperatures, and when it does, it will condense. This dampening dramatically decreases the thermal performance of the insulation and can promote mold and wood rot. To avoid this, a vapor barrier with a low perm rating must be installed.
The vapor retarder can be the kraft facing of an insulation product or it can be a separate layer placed on the interior side of the structure. The vapor retarder needs to be a low-permeable material, such as a cellulose, mineral wool or fiberglass facing, or a polyethylene film with a perm rating of less than 0.10 US perm. When choosing a vapor retarder, builders should consult with the manufacturer to verify the perm rating.
It is important to note that vapor retarders can be damaged during construction. Builders need to ensure that the vapor retarder is properly attached to all surfaces, and that any seams and punctures are sealed tightly with tape to maintain continuity. This is critical, especially in hot and humid climates where the vapor can travel across the insulation to the exterior face and cause condensation.
In most cases, a vapor retarder is required in the construction of framed wall assembly, especially for climate zones 5, 6, 7, 8, and marine 4 (see NAIMA’s ASHRAE climate zone map). However, builders can still use unfaced insulation in these zones, provided it is rated for the proper application.
In addition to being required in some climates, a vapor retarder is also necessary in slab-on-grade and basement wall applications. In these applications, a vapor retarder can significantly reduce the amount of moisture infiltrating into the slab and causing condensation and other problems. A vapor retarder should be used with a perforated metal facing in these situations. This allows vapor to pass through the metal, but prevents it from reaching the interior of the concrete floor and condensing.
Vapor Barrier Installation
Vapor barriers (also known as vapor retarders) are a critical part of wall and ceiling construction to prevent moisture from infiltrating the building envelope. By limiting the transfer of water vapor, vapor barriers protect structures from damage caused by moisture infiltration such as wood framing rot and mold and mildew.
In addition, properly installed vapor barriers can help maintain energy efficiency in a building and reduce operating costs by preventing warm air from being pulled into cold walls or ceilings. This can be particularly effective when paired with properly selected insulation materials to maximize the performance of both.
When constructing a building, the decision to incorporate a vapor barrier should be made based on local climate and the expected use of the structure. Building codes vary by region, and there are also professional guidelines established by organizations like the National Roofing Contractors Association to determine whether or not a vapor barrier is necessary for a project.
The type of vapor barrier required is based on the humidity level and temperature differences in a given area, with some regions having climates that require a more impermeable vapor barrier while others do not. In addition, the vapor barrier’s location within a wall can play an important role in its effectiveness. For example, homes located in warmer climates should install a vapor barrier closer to the interior surface of the wall to prevent warm, moisture-laden air from transferring to cold exterior walls and causing condensation.
To effectively ensure proper vapor barrier installation, it is best to hire a qualified building professional to complete the job. They will have the expertise and tools to complete the job efficiently while ensuring that it meets all relevant building standards and codes. In addition, a professional will have the necessary experience working in confined spaces such as crawl spaces, which can be hazardous without proper training.
Before commencing any work, it is crucial to thoroughly assess the space to be worked on and to make sure that all of the necessary materials are available. This includes plastic sheets for the vapor barrier, tapes and sealants, insulation materials and any other supplies needed for the project.